Comprehensive Guide to Temperature Sensors in Technology
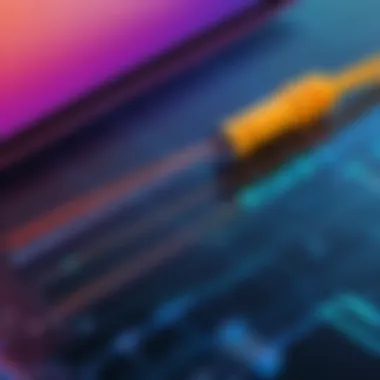
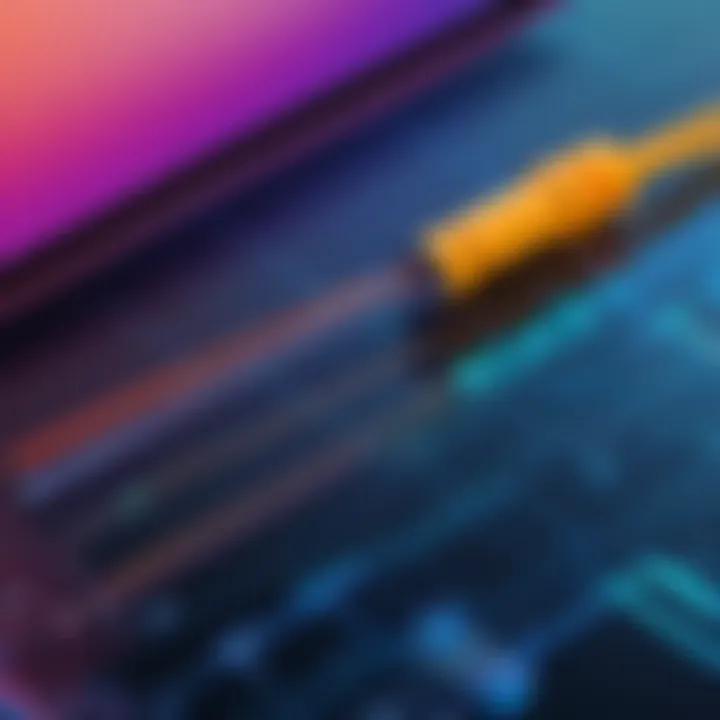
Intro
Temperature sensors have become crucial in today’s technology landscape. From small gadgets to large industrial systems, these sensors play a fundamental role in ensuring processes operate within desired temperature ranges. This article presents a comprehensive overview of temperature sensors, detailing their types, principles of operation, applications, advantages, and limitations.
As we navigate through this exploration, the aim is to deepen your understanding of these devices and facilitate informed decision-making in technology projects. The information serves engineers, programmers, and technology enthusiasts alike, providing a granular perspective on temperature sensors that goes beyond surface-level understanding.
Preface to Temperature Sensors
Temperature sensors play a crucial role in a variety of technological applications. Understanding them is essential for engineers and researchers alike, as they provide vital information necessary for many systems. This section introduces the fundamental aspects of temperature sensors, emphasizing their significance in both everyday life and specialized industries.
Definition and Importance
A temperature sensor is a device that detects temperature changes and converts them into readable signals. These signals can be analog or digital. They are important because they allow for accurate monitoring and control of temperature in environments ranging from household appliances to industrial machines.
One key aspect is their ability to gather data in real time. Temperature sensors can operate under different conditions, making them adaptable to various needs. They serve critical roles in safety, efficiency, and data accuracy across multiple sectors.
In addition to their operational significance, the quality and type of temperature sensors chosen can greatly impact the results of experiments and functioning of devices. This shapes decision-making processes in technology development and implementation.
Applications in Various Fields
The applications of temperature sensors are expansive, touching numerous sectors. Some noteworthy fields include:
- Industrial Automation: Temperature readings influence machinery and system performance. Sensors help in maintaining optimal operational conditions, promoting efficiency and safety.
- Environmental Monitoring: Sensors measure external temperatures, providing essential information for climate studies and art conservation efforts.
- Healthcare: In medical settings, temperature sensors monitor patient vitals, ensuring safety and quick response to abnormalities.
- Consumer Electronics: Devices like refrigerators, ovens, and HVAC systems utilize temperature sensors for effective operation, enhancing user comfort and device longevity.
The broad array of applications highlights the significance of understanding temperature sensors thoroughly.
Recognition of how temperature sensors function and their diverse uses allows technology enthusiasts and professionals to make informed choices. This understanding is key to leveraging their advantages in practical contexts, driving innovation and improved results.
Fundamental Types of Temperature Sensors
Temperature sensors are essential components in various technoligies, providing vital data that is utilized in countless applications. Understanding these fundamental types helps grasp how they function and their roles in industry and academia. This section delves into two primary categories: contact and non-contact temperature sensors. Each type brings unique elements, advantages, and contemplation points.
Contact Temperature Sensors
Contact temperature sensors are devices that measure temperature by direct contact with the object being measured. Thes sensors are commonly employed when sensors must show accurate readings of solid surfaces or liquids. Their use is widespread and can be found in HVAC systems, manufacturing processes, and scientific research applications. Key forms of these sensors include thermocouples and resistance temperature detectors.
Some benefits of contact temperature sensors include:
- High Accuracy: These sensors often provide high precision readings due to direct contact.
- Wide Temperature Range: Many contact sensors can withstand extreme temperatures, making them versatile for various operations.
- Variety of Designs: With technological advances, contact sensors have diversified into several designs, accommodating diferent use cases.
Nonetheless, they do have limitations. For instance, they can be subjected to wear and tear, corrosion, and can be unsuitable for measurements where physical contact is not practical.
Non-Contact Temperature Sensors
Non-contact temperature sensors, as their name implies, measure temperature without any physical contact with the objects. The principle behind these sensors primarily relies on the detection of emitted infrared radiation from an object’s surface. They are used extensively in medical applications, to prevent contamination, as well as during the monitoring of temperatures in moving objects or scenarios where contact is not feasible.
There are notable characteristics for these types sensors:
- Temperature Range: They can measure temperatures in extreme ranges effectively, very dificult situations for contact sensors.
- Safety: By avoiding physical contact, they minimize risks associated with dangerous or hazardous materials.
- Real-Time Monitoring: Non-contact sensors enable continuous monitoring without disturbing the process or the subject being evaluated.
However, non-contact sensors also come with specific constraints. Environmental factors, such as dust, smoke, or obstacles, may hinder their accuracy. Furthermore, assuming the emissivity factor of the material can lead to errors in the readings.
Both contact and non-contact sensors play vital roles in advancing modern technology, giving opportunities for precise temperature control and enhancing overall efficiency.
Overall, understanding the fundamental types of temperature sensors is crucial for engineers and technologists aiming to select the most appropriate solutions for their projects. Each category brings distinct features and capabilities, influencing decisions on method and implementation.
Thermocouples
Thermocouples are central to the topic of temperature sensors, given their widespread use and effectiveness in measuring temperatures across various environments. Thermocouples work on the principle of generating a voltage corresponding to the temperature difference between two junctions made from dissimilar metals. This simplicity is part of what makes them popular in many applications, from industrial settings to laboratory usage. They are especially valued for their ability to withstand high temperatures and provide relatively quick response times.
Principle of Operation
The operating principle of a thermocouple is based on the Seebeck effect. This phenomenon occurs when two different metallic conductors form a junction and generate a voltage in response to a temperature difference between the junctions. Two junctions are present—one placed at the temperature to measure, called the measuring or hot junction, and the other held at a reference temperature, known as the cold junction.
The voltage generated can be reliably correlated to the temperature difference, allowing for precise measurements. However, the accuracy of this method is influenced by several factors, including the materials' thermoelectric properties and ambient conditions.
Types of Thermocouples
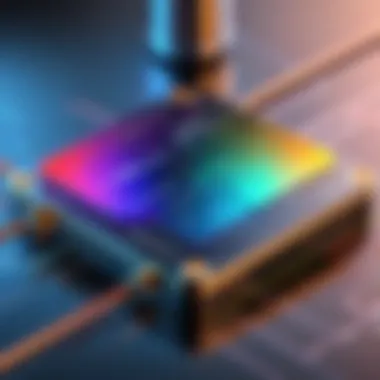
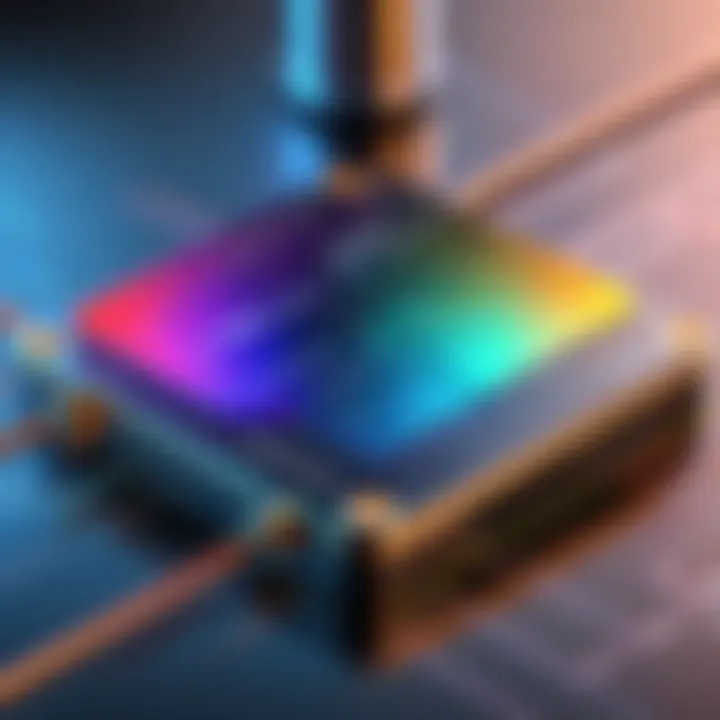
Type K
Type K thermocouples are among the most commonly used types. They are crafted from chromel (nickel-chromium alloy) and alumel (nickel-alumel alloy) materials. One key aspect of Type K thermocouples is their broad temperature range, functioning effectively between -200 to 1260 degrees Celsius. Their stability and resistance to oxidation make them a beneficial choice in many industrial applications such as heat treatmnet and furnace operations. However, they may not perform well in some situations below zero or in areas with strong electromagnetic interference.
Type J
Type J thermocouples are composed of iron and constantan (a copper-nickel alloy). They have a maximum temperature rating of 750 degrees Celsius. A notable chracteristic is their Magnetic property causing thermoelectric measurements in certain environments to be more complicated. Although they work well in vacuum or inert environments, they are not usually recommended for high temperature applications due to oxidation risks of the iron wire.
Type T
Type T thermocouples utilize copper versus constantan wires similar to Type J but are configurable for lower temperature ranges, typically from -200 to 350 degrees Celsius. Their characteristics prove particularly valuable in food and pharmaceutical industries, where low-end precision is required. The key advantage is their increased accuracy in temperatures below freezing, which stands out in certain analytical applications. Nevertheless, caution is needed due to their susceptibility to electromagnetic fields that influence electrical signals.
Type E
Type E thermocouples use nickel-chromium versus constantan wires defining them with an extended maximum temperature capacity of about 900 degrees Celsius. They display a higher output voltage to temperature response ratio which advances sensitivity, making them ideal for elaborate temperature tests where precision is crucial. While this type is excellent for oxidation resistance, caution must be exercised in high temperatures as their iron component may degrade the readings.
Advantages and Limitations
Thermocouples possess distinct advantages such as a wide operating temperature span, inexpensive materials, and robust construction suited for severe environments. Some limitations include lower precision compared to other types like RTDs, environmental restrictions leading to calibration error, and non-linear output voltage which requires additional processing for accurate readings.
Resistance Temperature Detectors (RTDs)
Resistance Temperature Detectors, commonly known as RTDs, play a crucial role in the realm of temperature measurement, offering a precise and reliable method to gauge temperature changes. They are preferred in various industrial applications due to their accuracy, stability, and repeatability. Understanding RTDs is vital for engineers and technicians who work with temperature sensing devices, as they form the backbone for systems reliant on exact temperature data.
Construction and Working Principle
RTDs consist of a sensing element, terminal connections, and a protective casing. The sensing element is typically made of a metal such as platinum, which changes its electrical resistance in response to temperature variations. This change in resistance can be correlated with a determined scale for temperature, enabling accurate readings.
The most common RTD configuration is the wire-wound RTD. It is constructed by wrapping a fine wire around a ceramic or glass core. As the temperature increases, the wire's resistance increases proportionally. Another variant is the thin-film RTD, where a thin layer of metal is deposited onto a substrate, allowing for quicker response times.
Working Principle Summary:
- Resistivity Change: Changes in temperature cause the metal's resistivity to change.
- Resistance Measurement: The overall resistance is measured using electrical circuits.
- Calibration: A known correlation exists between resistance and temperature, providing an accurate output.
Applications and Suitability
RTDs are widely used in applications where precision is paramount. Their operation is most suited for instances needing stable measurements over extended periods. Common uses encompass:
- Industrial Process Control: Ensuring optimal operating temperatures in manufacturing processes.
- Food Processing: Monitoring temperatures in pasteurization and refrigeration.
- Scientific Research: Providing precise temperature data for experiments in laboratories.
The reliability and accuracy of RTDs make them ideal for sensitive equipment such as thermoregulated reactors and HVAC systems. Nevertheless, designers must consider their suitability based on the project specifications. Cost and environment are crucial factors influencing the decision on deploys RTDs.
Comparison with Thermocouples
When examining temperature sensors, both RTDs and thermocouples often arise as primary solutions. However, their working mechanisms, advantages, and limitations differ markedly.
- Accuracy: RTDs tend to offer higher accuracy than thermocouples, with precision often better than 0.1°C.
- Temperature Range: Thermocouples can measure extreme temperatures, whereas RTDs usually function effectively within a limit of -200°C to 850°C.
- Response Time: Thermocouples generally demonstrate faster response times due to their construction, which can be crucial in dynamic systems.
- Stability: RTDs exhibit superior stability over time compared to thermocouples, making them favorable for long-term temperature monitoring.
Ultimately, the decision between RTDs and thermocouples is driven by project requirements, including precision needed and operating conditions. Each sensor offers distinct advantages, ensuring that both types hold significant places in temperature sensing technologies.
Thermistors
Thermistors are an essential type of temperature sensor that play a significant role in modern temperature measurement applications. Their unique characteristics make them suitable for a variety of uses. Understanding thermistors involves appreciating their fundamental properties, various types, and the specific applications in which they excel.
Characteristics and Response
A thermistor's response to temperature changes is based on its resistance, which varies significantly with temperature. This sensitivity allows them to detect small fluctuations in temperature accurately. Thermistors operate on the principle of resistance change with temperature, which is not linear, adding to their complexity but also making them quite effective for precise measurements in specific ranges. The high degree of non-linear response makes thermistors highly suited for applications such as temperature control and regulation.
Types of Thermistors
Thermistors are categorized mainly into two types: NTC (Negative Temperature Coefficient) and PTC (Positive Temperature Coefficient). Each of these thermistors possesses distinct properties and applications that make them uniquely suited for different tasks.
NTC (Negative Temperature Coefficient)
NTC thermistors show a decrease in resistance with increasing temperature. This property makes them widely popular in many applications, such as temperature sensing and circuit protection. Their main edge lies in the sensitivity to minute shifts in ambient temperature. For instance, NTCs can deliver precise readings needed in medical devices like digital thermometers for patients. However, they may face limitations at higher temperature ranges, showing reduced accuracy due to their design.
PTC (Positive Temperature Coefficient)
In contrast, PTC thermistors have a behavior where their resistance increases with an increase in temperature. These are exceptionally effective in applications where overload protection is essential. Due to their characteristics, PTCs are used in circuit protection components, ensuring electronic devices do not overheat. While PTCs offer benefits in protection, they might be less sensitive than NTCs in measurement tasks where accuracy is paramount.
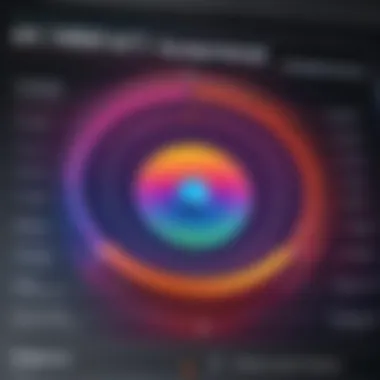
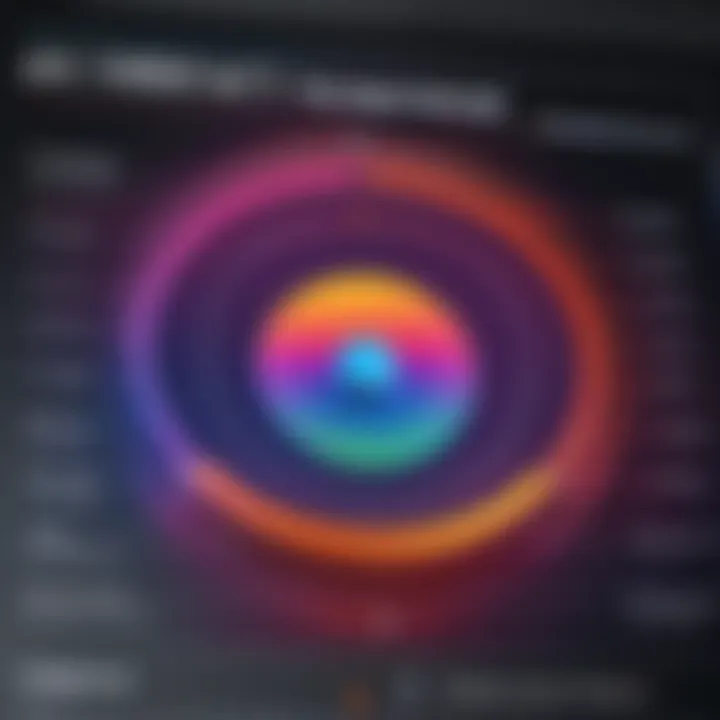
Common Applications
Thermistors find usage in a wide range of fields. Some common applications include:
- Medical devices (such as patient monitoring devices and thermometer)
- Automotive temperature monitoring
- HVAC systems for precise temperature control
- Consumer electronics, like refrigerators and air conditioners
Their versatility makes them inherently important in protecting sensitive components across various industries.
Infrared Temperature Sensors
Infrared temperature sensors have gained significant recognition for their unique ability to measure temperature from a distance. This capability not only makes them ideal for various applications but also outweighs many problems associated with traditional contact sensors. Their relevance in numerous fields shines light on the evolvement of temperature measurement technologies, offering benefits that enhance operational efficiency and safety.
Operating Principles
Infrared temperature sensors operate based on the principle of detecting the infrared radiation emitted by an object. Every warm object releases infrared radiation, which is proportionate to its temperature. The sensor contains a lens to focus this radiation onto a detector, which converts it into an electrical signal. This signal is then processed to provide a readout in temperature units like Celsius or Fahrenheit.
A variety of technologies underlie these sensors, including thermopiles, photodetectors, and pyroelectric sensors. Each type has unique attributes but fundamentally relies on the detection of infrared radiation. Crucially, accurate measurements depend on calibration factors to account for emissivity, or how effectively a surface emits infrared energy.
Advantages in Non-Contact Measurements
One of the most notable advantages of infrared temperature sensors is their non-contact measurement capability. Unlike traditional methods, they do not need to touch the surface whose temperature is being measured. Benefits of this include:
- Safety: Ideal for hazardous materials where direct contact might pose risks to both the instrument and the operator.
- Speed: Measurements are almost instantaneous, making them suitable for processes requiring rapid responses.
- Versatility: Can measure temperature in hard-to-reach areas without causing disruption but remain within a safe distance.
- Real-time monitoring: Perfectly adept in instances where continuous monitoring is necessary, like conveyor belts in manufacturing.
The reduction in wear caused by contact means enhanced instrument durability leading to lower long-term replacement costs and maintenance needs.
Common Use Cases
Infrared temperature sensors serve a wide range of applications across different industries, reflecting their versatile nature. Some common use cases include:
- HVAC systems: Check temperatures of ducting and ambient environments to maintain and increase efficiency of climate control.
- Medical devices: Used in thermometers for measuring body temperature without physical contact. This application gained traction during health crises, making it a favored choice.
- Manufacturing: Monitor equipment and processes without interference, ensuring more stable conditions favoring consistent quality of products.
- Automotive applications: Employed to monitor engine temp and for monitoring brakes, helping ensure vehicle safety.
- Food inspection: Critically used in food safety inspection processes to quickly measure surface temperatures.
To summarize, infrared temperature sensors operate on principles of non-contact infrared radiation detection, offering speed and versatility for various applications such as HVAC systems, medical devices, and industrial monitoring. Their capability ensures both efficiency and safety, highlighting their place in modern temperature measurement technology.
Bimetallic Temperature Sensors
Bimetallic temperature sensors represent a smart alternative for temperature measurement, relying on the principle of differential expansion between two different metals. It is crucial to understand these sensors as they play an essential role in temperature management across various applications and industries. The design of bimetallic strips translates thermal variations into motion, providing simple solutions for monitoring thermal environments. In contexts where you need straightforward and reliable temperature data, bimetallic sensors shine with their durability and efficacy.
Construction and Working Mechanism
The construction of bimetallic temperature sensors involves bonding two different metallic strips. One of the common metal pairs includes brass and steel. These two materials feature different rates of thermal expansion. When exposed to temperature changes, one metal expands more than the other. This unequal expansion causes the bimetallic strip to bend.
As the temperature increases, the strip curves, and the displacement can be visually read or instrumentally measured. As it bends, it may trigger switches or dials to provide the actual temperature reading. This is often displayed on mechanical gauges and sometimes integrated into more complex monitoring systems.
Applications in Industry
Bimetallic temperature sensors are ubiquitous in various industries. Here are some key applications:
- HVAC systems: Used to measure the inside temperatures and regulate climates effectively.
- Automotive: Common in gauges for tire pressure and engine coolant assessment.
- Manufacturing: Vital in processes where keeping specific heat levels is crucial for product quality.
- Home appliances: Often found in thermometers and thermostats, giving consumers immediate feedback about temperatures.
Their reliability and low cost make them a preferred choice for non-critical measurements where high accuracy is not paramount.
Pros and Cons
Like any technology, bimetallic temperature sensors come with their strengths and weaknesses.
Pros:
- Simplicity: Their design is often uncomplicated, which makes installation easy.
- Durability: They can withstand various environmental conditions.
- Cost-Effective: Generally less expensive than electronic sensors.
Cons:
- Accuracy: Less accurate than thermocouples or RTDs in high-precision applications.
- Speed: Response time can be slower due to mechanical movement compared to electronic sensors.
Bimetallic sensors are a reliable choice where functionality meets economy.
Gas Thermometers
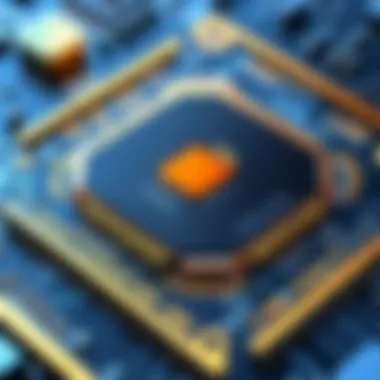
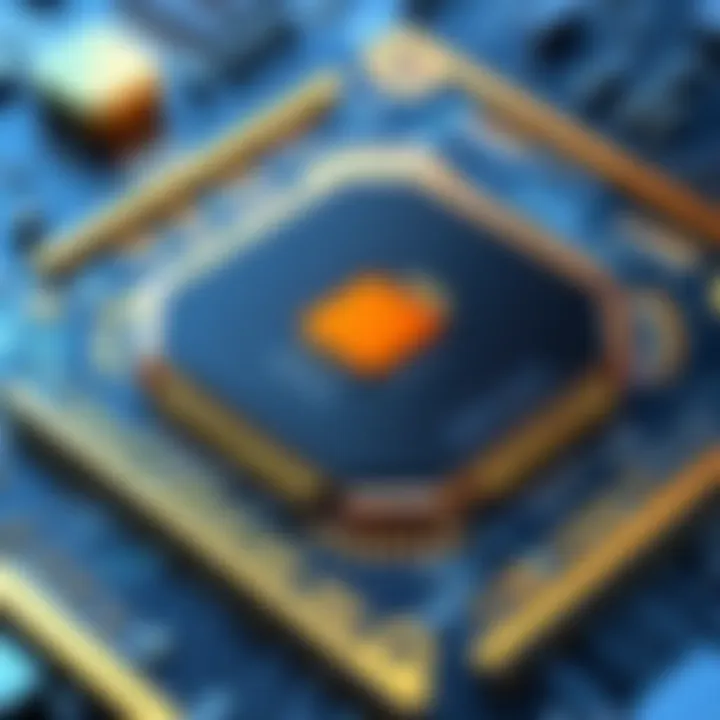
Gas thermometers are notable for their precision in measuring temperature, particularly in scientific applications. They utilize the principle that gases expand when heated and contract when cooled, a fundamental physical property that has been harnessed for centuries. Their ability to accurately reflect changes in temperature makes them crucial tools in various fields ranging from laboratory settings to industrial processes.
Principle of Temperature Measurement
The principle behind gas thermometers revolves around the thermal expansion of gases. As the temperature rises, the kinetic energy of gas molecules increases, leading to greater molecular motion and expansion of the gas. A gas thermometer typically consists of a sealed glass container which is partially filled with a specific gas like nitrogen or helium. This container is attached to a calibrated scale that indicates temperature based on the gas's volume displacement. The relationship between temperature, pressure, and volume is described by the ideal gas law, enabling precise temperature readings. This approach allows for highly accurate measurements.
Consider the accuracy of a gas thermometer:
- Calibration: Details in the calibration process ensure accuracy.
- Material Dependence: Different gases can influence sensitivity and response rates.
- Lower Temperature Range: Gas thermometers operate well in lower temperature ranges, enhancing reliability.
Applications and Effectiveness
Gas thermometers are employed mainly in scientific research and environments where precision is crucial. Their widespread applications include:
- Laboratory Research: Essential in experiments requiring accurate temperature monitoring.
- Quality Control: Used in manufacturing processes where temperature stability is vital.
- Meteorology: Plays a role in measuring temperatures in standard reference conditions.
The effectiveness of gas thermometers stems from their response to temperature changes, typically over a wide range, making them useful in harsh conditions. Also, they are less affected by external factors such as electrical interference. This characteristic makes gas thermometers a wise choice in industries relying on accuracy.
Limitations of Gas Thermometers
While gas thermometers excel in measurement accuracy, they come with certain limitations. Some notable drawbacks include:
- Sensitivity to Changes in Pressure: Variations in atmospheric pressure can result in erroneous readings.
- Bulkiness: The structure of gas thermometers may limit their portability when compared to electronic sensors.
- Temperature Range Constraints: Limited effective measurement range, making them unsuitable for extremely low or high temperatures.
In certain conditions, other types of temperature measurement devices may provide better alternatives. For instance, thermocouples or resistance temperature detectors (RTDs) may perform more effectively in environments with extreme temperatures or where rapid response times are necessary.
"Although gas thermometers provide great accuracy, understanding their limitations can help in selecting the appropriate temperature sensing device."
Emerging Technologies in Temperature Sensing
Emerging technologies in temperature sensing play a critical role in the evolution of industries relying heavily on precise measurements. The increasing demand for efficiency and accuracy is pushing the bounds of what traditional sensors can achieve. These innovative technologies not only enhance the functionality but also offer valuable integrative capabilities for more sophisticated monitoring systems. With advancements in materials and electronics, the landscape of temperature sensing is rapidly changing. This section discusses key aspects of smart sensors, IoT integration, future trends, and challenges faced in this evolving field.
Smart Sensors and IoT Integration
Smart sensors represent a new frontier in temperature sensing technology. They are designed to provide real-time data transmission, minimizing the need for manual monitoring. These sensors utilize internet connectivity and sophisticated algorithms to analyze temperature data dynamically. As a result, smart sensors can adjust their operations based on environmental changes rather than working in isolation.
The integration of these smart sensors into broader Internet of Things (IoT) networks presents significant benefits:
- Enhanced data accuracy and reliability through real-time readings.
- Reduced operational costs by enabling predictive maintenance and reducing down-time.
- Improved user interfaces allowing for remote monitoring and control.
In practical terms, industries such as agriculture and manufacturing use smart temperature sensors. They enable automated irrigation, climate control, and maintenance scheduling. This integration elicits a shift in how temperature measurements fuel not just efficiency but also adaptive operational protocols. The result is smarter systems that can thrive in the complexities of modern demands without compromising performance.
Future Trends and Challenges
As temperature sensors become more sophisticated, several trends and challenges are evident. Future developments will likely focus on:
- Miniaturization: Smaller sensors with advanced capabilities for placement in restricted environments.
- Sustainability: Development of energy-efficient sensors reducing battery dependence and promoting eco-friendliness.
- Enhanced Connectivity: Improved protocols for seamless data transfer among various sensor types and devices.
However, several challenges accompany these promising trends. Key issues include:
- Data Security: With IoT’s expansion, protecting sensor data from unauthorized access is paramount.
- Interoperability: Ensuring diverse sensor types and brands work seamlessly requires standardization.
- Accuracy in Diverse Conditions: Maintaining precise readings across varying climates and workflows presents ongoing hurdles.
The future landscape of temperature sensors is deeply connected to advancements in smart technologies and IoT integration.
Addressing these challenges will be crucial for realizing the full potential of emerging temperature sensing technologies, making it an area ripe for innovative solutions. Stakeholders must hence invest in research and development for sustainable practices while navigating through the uncertainties inherent in technological advances.
End
The conclusion serves as a crucial component of this article, synthesizing the pivotal elements and insights gained from our exploration into various temperature sensors. In a landscape where technology continually evolves, the knowledge of different types and functionalities of temperature sensors is paramount for engineers and technology enthusiasts alike. The scope of this article illustrates these devices' principles, applications, and respective strengths and weaknesses, all of which play an essential role in fostering informed decision-making.
Summary of Key Insights
Throughout this detailed examination of temperature sensors, several key insights come forward:
- Broad Spectrum of Sensors: There exists a variety of temperature sensors such as thermocouples, RTDs, thermistors, and infrared sensors, each engineered for specific applications.
- Operational Principles: Understanding the working principles of each sensor type allows for more informed choices in their respective use cases. For instance, thermocouples excel at handling extreme temperatures, while RTDs tend to offer superior accuracy.
- Applications: Various fields utilize temperature sensors, including healthcare, industrial sectors, and consumer electronics. Each application requires tailored sensors.
- Emerging Technologies: The intersection of temperature sensing with smart technology and IoT integration illustrates the forward trajectory of the sensor industry.
- Challenges Ahead: Despite advancements, challenges still present themselves, such as calibration issues and susceptibility to environmental factors.
These insights not only underline the importance of temperature sensing technology but also highlight the vital role it plays across multiple domains, from comforting a patient in healthcare to ensuring quality control in manufacturing processes.
Implications for Future Research and Development
Temperature sensors are pivotal to future advancements in technology and industrial applications. Several avenues for further research and development reveal untapped potential:
- Enhanced Precision: As industries demand increasingly precise measurements, ongoing advancements in sensor materials and designs could lead to significant enhancements in accuracy and reliability.
- Smart Integration: Continued research on IoT-enabled sensors can potentially revolutionize remote monitoring systems, enabling real-time data access and increased systematic efficiencies.
- Energy Efficiency: Development of low-power temperature sensors suitable for battery-operated devices will be crucial in quickly growing markets such as wearables.
- Material Innovation: Investment in new materials could result in sensors operating in harsher environments without compromising functionality or cost-effectiveness.
As we navigate into a technologically advanced era, the intersection of temperature sensing with digital innovations will continue to hold tremendous potential for improving operational efficiencies and refining measurement accuracy in complex systems. These factors underline the need for ongoing research aimed at tackling existing limitations while exploring newly emerging technologies.