Exploring the Evolution and Impact of Manufacturer Resource Planning
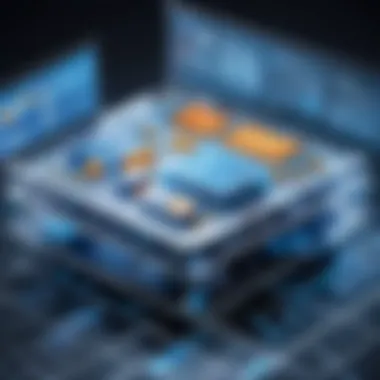
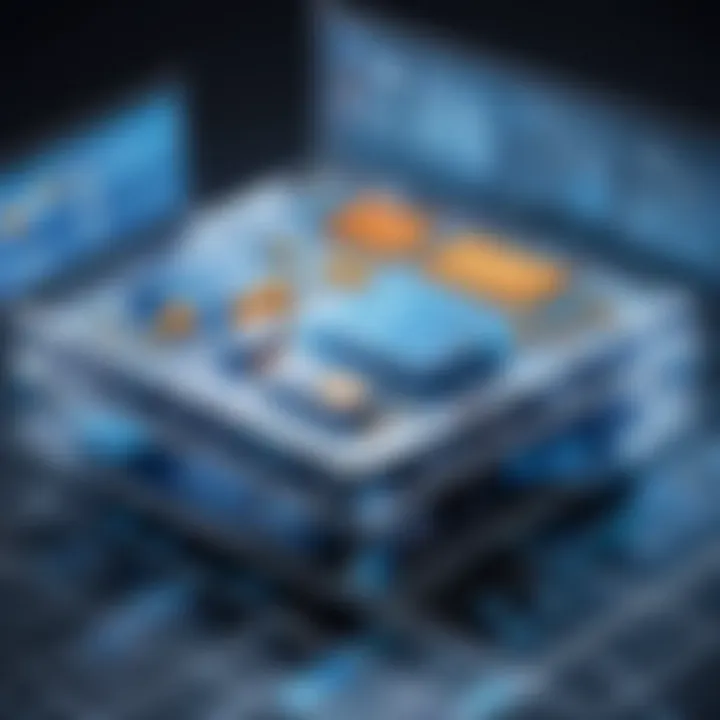
Intro
Manufacturer Resource Planning (MRP) is pivotal in today's manufacturing landscape, bridging the gap between efficient production processes and effective inventory management. As manufacturers strive for operational excellence, understanding MRP concepts becomes essential. This section serves as an introduction to MRP, emphasizing its importance and relevance in the modern manufacturing environment.
Understanding MRP encompasses various elements, from its historical context to advancements brought upon by technology. Incorporating software systems and data analytics reflects the uniqueness of MRP in enhancing productivity. Additionally, recognizing its integration with supply chain management showcases MRP's holistic approach.
Several trends are radically affecting how manufacturing operates, and MRP adapts to these changes swiftly. By delving deeper into MRP fundamentals and their implications, industry professionals can gain insights vital for maintaining competitive advantages.
Key Points of Discussion
- Fundamental Principles of MRP: A look into what makes MRP indispensable for modern manufacturers and the core concepts underlying it.
- Historical Evolution: The trajectory of MRP from its inception to current incarnations, reflecting on significant milestones.
- Technological Advancements: Evaluation of technological integrations revolutionizing MRP, focusing on inventory management and forecasting accuracy.
- Challenges and Opportunities: Identifying potential pitfalls in MRP systems, while also outlining the new opportunities emerging from them.
In subsequent sections, we will dive closely into each aspect mentioned above, contributing towards defining a comprehensive understanding of Manufacturer Resource Planning.
Understanding Manufacturer Resource Planning
Understanding Manufacturer Resource Planning (MRP) serves as a keystone for improving production efficiency and achieving cohesive operations within manufacturing settings. Recognizing this framework's fundamental role is essential for modern manufacturers aiming to enhance their systems and maintain competitive advantage in an increasingly complex market.
Definition of MRP
Manufacturer Resource Planning (MRP) can be defined as a systematic method for managing manufacturing processes through the planning, scheduling, and inventory control of materials required in production. It offers a structured approach to efficiently coordinate various components of manufacturing, including raw materials, production equipment, and labor resources. MRP uses data on product demand to forecast materials needed and schedule their procurement, ensuring that materials will be available when needed throughout the production cycle.
Importance of MRP in Manufacturing
The significance of MRP in manufacturing cannot be overstated. Here are some vital points highlighting MRP's impact:
- Streamlined Operations: MRP enhances production processes by optimizing the use of resources. When properly implemented, it ensures that the right quantity of materials is available at the correct time, thus facilitating smoother operations.
- Cost Control: With reduced excess inventory and minimized waste, MRP leads to significant cost savings. It aligns production schedules with order demands, reducing both carrying costs and the potential for obsolescence.
- Reduced Lead Times: By planning materials more efficiently, manufacturers can significantly decrease lead times. Quick responses to changes in demand enable businesses to react faster and meet customer needs.
- Enhanced Planning Capabilities: MRP enables better forecasting and demand planning, providing manufacturers with critical insights necessary for strategic decision-making. Accurate data collection improves overall manufacturing agility.
"MRP is a framework that, when leveraged effectively, enables manufacturers not just to survive but to thrive amid evolving market demands."
Historical Overview of Manufacturer Resource Planning
Understanding the historical context of Manufacturer Resource Planning (MRP) provides significant insights into its current applications and advantages. This section emphasizes past developments in resource planning, serving as a foundation for comprehension of modern MRP systems. Additionally, historical reflection helps in identifying common pitfalls that practitioners faced and resolved, contributing to the ongoing improvement of MRP methodologies.
Early Concepts of Resource Planning
Resource planning originated from the necessity to streamline manufacturing processes. Early methods were rudimentary, focusing primarily on basic materials control. These concepts included simple spreadsheets, manual stock taking, and rudimentary forecasting based upon historical data. Though they laid the groundwork for efficiency, issues like inaccuracies and delays persisted due to reliance on manual data entry.
In the mid-20th century, lean principles began to emerge. This influenced manufacturers to shift from traditional inventory methods to just-in-time systems. JIT advocated minimizing stock levels while ensuring that production would run smoothly. The focus on worker involvement and continuous improvement highlighted the need for systematic planning.
- As manufacturing grew in complexity, the inadequacies of early techniques became evident. Academic theorists and operations managers recognized the need for a more structured approach, leading to significant evolution in thinking about resource allocation and enterprise-wide solutions.
Evolution of MRP Systems
The term
Key Components of MRP
The foundational aspects of Manufacturer Resource Planning are essential for optimizing efficiency. Each component plays a significant role in the framework of MRP. Understanding these components is essential for industry professionals who seek details on effectively managing resources. This section will discuss inventory management, production scheduling, and demand forecastingโthree critical elements within MRP that harness information to better streamline operations.
Inventory Management
Inventory management is a key element of MRP. It involves monitoring of all stocks, raw materials, and finished goods within the manufacturing process. The main aim is to ensure that adequate supplies are available when needed while minimizing excess surplus. Having a balanced inventory takes skill and strategy. Here are some benefits of well-structured inventory management:
- Reduced costs through minimizing carrying and storage expenses.
- Improved order fulfilment that enhances customer satisfaction.
- Minimized waste by avoid expired or obsolete goods.
MRP systems allow businesses to track quantities and devise reorder points, which helps prevent bottlenecks in production. For any enterprise, missing inventory could lead to lost sales and depressed brand reputation. Hence, mindful inventory management facilitates better operational flow.
Production Scheduling
Production scheduling ensures that all manufacturing activities are aligned and run smoothly. It determines how resources, people, and timescales are utilized. Effective scheduling maximizes production efficiency while minimizing downtime. Key considerations in production scheduling include:
- Capacity planning: Identifying the overall capacity required to produce goods.
- Sequence of activities: Ensures tasks are organized logically.
- Prioritization of orders: Custom or urgent orders are processed as needed.
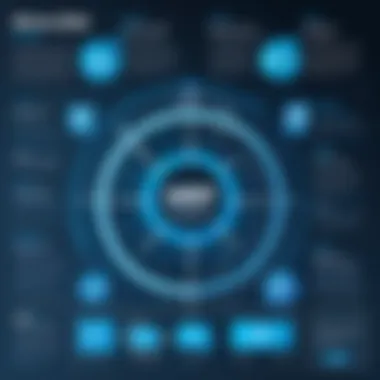
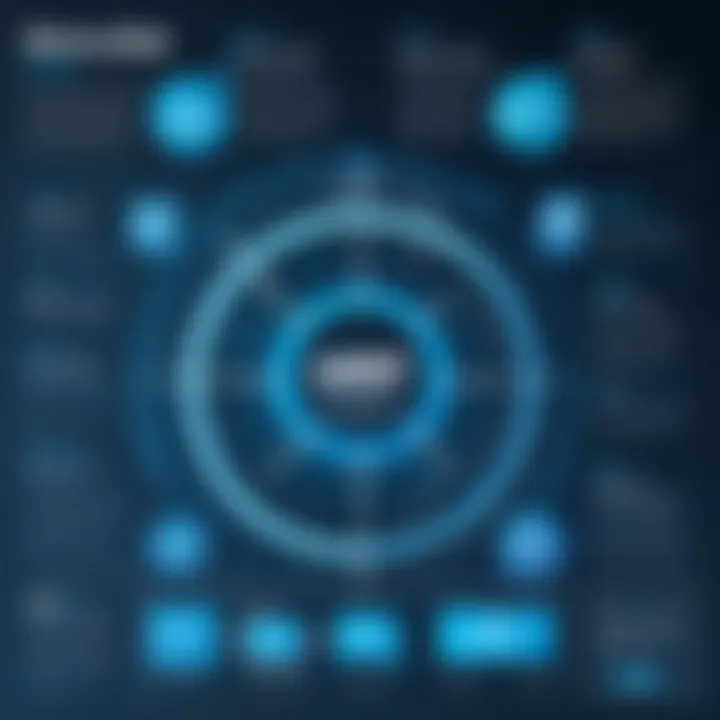
Adopting solid production scheduling methods can lead to an enhanced operational environment and lower costs. Disruptions in production can cascade into larger issues without proper foresight and strategizing. Thus, manufacturers using MRP tend to achieve streamlined processes that cater to timely delivery.
Demand Forecasting
Lastly, demand forecasting acts as a compass, guiding businesses on how much product to manufacture. Using historical sales data, market analysis, and trends, accurate forecasting informs the overall production plan. Essential aspects of demand forecasting include:
- Analysis of customer trends: Understanding what the customer desires helps in designing products that match expectations.
- Seasonal considerations: Recognizing seasonal changes enables better position of stock.
- Collaborative input: Gathering insights from various departments leads to more robust forecasting.
The effectiveness of demand forecasting directly correlates to business success. Prices of raw materials and lead times can fluctuate; hence being prepared with accurate predictions safeguards against variance in business operations. It assists manufacturers on producing just enough while minimizing both excess and shortage.
In summary, the key components of MRP reveal the intricate cogs operating within a defined system. When utilized mindfully, Companies are well-equipped to make resource-driven decisions leading to superior operational outcomes.
The Role of Technology in MRP
Technology serves as a catalyst in the realm of Manufacturer Resource Planning (MRP). It not only enhances the capabilities of MRP systems but also streamlines various processes within manufacturing organizations. The adoption of advanced technology creates a framework for better efficiency, superior data management, and integrated systems which are essential in todayโs competitive market.
Advanced MRP software aids businesses in synchronizing their materials, labor, and production schedules. This leads to reduced lead times and waste in production. As organizations become increasingly reliant on precise data and forecasting tools, technology's role transforms from optional to essential. This section examines how technology integrates into MRP, from software solutions to advanced data analytics. Let's look closer at each component here.
Software Solutions
Software stands at the forefront of MRP technologies. Solutions such as SAP S/4HANA and Oracle NetSuite provide critical tools for managing resources effectively. These platforms offer features that assist businesses in tracking order management, understanding inventory status, and forecasting demand requirements. As a result, decision-making becomes data-driven, reducing reliance on intuition or outdated methods.
Some key benefits of these software solutions include:
- Real-time Data Access: Immediate updates on inventory levels, production schedules, and supply chain efficiency.
- Customization Options: Tailored functionalities that adapt to the unique needs of different industries.
- User-Friendly Interfaces: Simplified navigation which allows team members to become proficient quickly.
Overall, software solutions fortify the MRP system and improve operational workflows significantly.
Cloud Computing and MRP
Embracing cloud computing is a notable shift for the manufacturing sector regarding MRP. Using platforms such as Microsoft Azure and Amazon Web Services (AWS) provides practitioners with scalable resources and flexibility. When compared to traditional on-premises setups, cloud solutions reduce IT costs and infrastructure concerns.
Additionally, cloud computing has various advantages, including:
- Accessibility: Team members can access data and tools from any location, fostering collaboration across different geographical locations.
- Cost Efficiency: Lowered upfront costs, allowing businesses to pay as they grow.
- Automatic Updates: Regular software updates ensuring facilities implement current features without manual intervention.
As a consequence, the role of cloud computing in MRP is paramount for ensuring uptime and responsiveness.
Integration with Other Systems
The seamless integration of MRP systems with other applications is crucial for operational coherence. Many plants are utilizing integrated systems such as Customer Relationship Management (CRM) software and Enterprise Resource Planning (ERP) suites. This interlinking creates a holistic view of operations.
Advantages of integration include:
- Unified Data Flows: Each section of business, from inventory to sales, maintains accurate and consistent information throughout the system.
- Enhanced Collaboration: Cross-departmental visibility improves communication and decision-making prompts.
- Improved Response Times: Facets of production align closer to both demand and operation requirements, leading to increased overall responsiveness.
The integration of systems not only compresses management processes but cultivates adaptability, which is essential in today's fast-paced market.
The essence of technology in MRP is its ability to enhance oversight of production and resource allocation, which directly influences profitability and efficiency plans.
Data Analytics in MRP
Data analytics has become a cornerstone of Manufacturer Resource Planning (MRP), offering insights that drive decisions and streamline operations. Understanding how data informs various aspects of manufacturing is crucial for both efficiency and effectiveness.
Role of Data in Decision Making
Effective decision-making in manufacturing relies heavily on data. MRP systems gather vast amounts of information from production processes, inventory levels, and customer demand, creating a comprehensive data landscape. This data not only aids in day-to-day operations but also shapes long-term strategies.
Decisions backed by data tend to be more accurate and nuanced. For example, using historical sales data can help manufacturers forecast future demand with greater precision. This reduces the risk of overproduction or stockouts, ultimately leading to cost savings and improved resource allocation.
Key data types utilized in decision-making include:
- Sales trends: Analyzing past sales helps anticipate future demand.
- Inventory levels: Monitoring stock levels informs replenishment strategies.
- Production data: Insights from production efficiency guide protocols and processes.
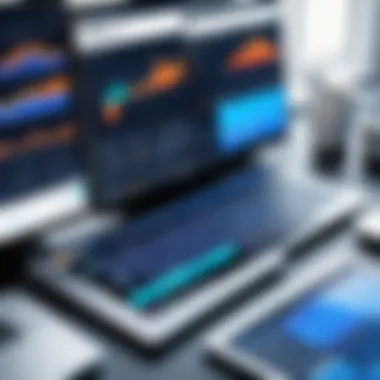
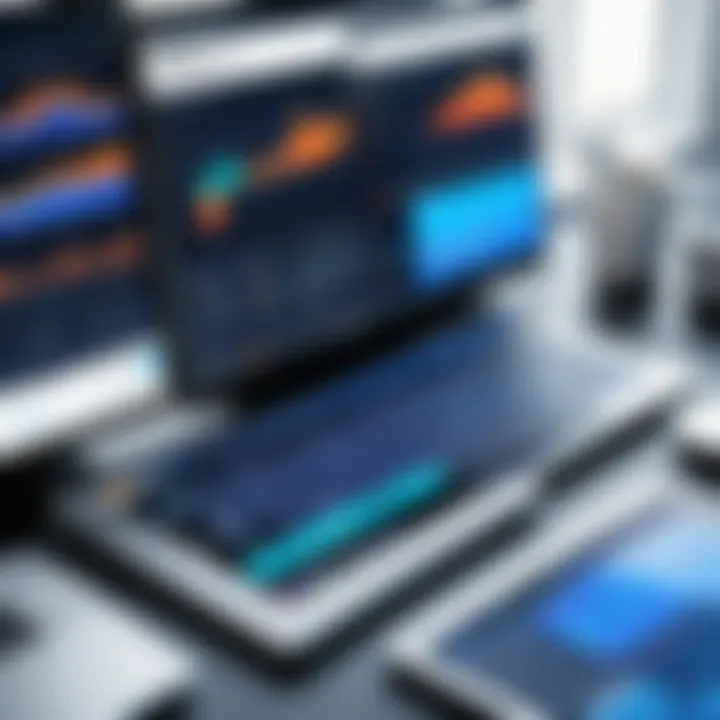
The emphasis on data-driven decision-making ensures a proactive approach instead of a reactive one. Therefore, data analytics plays a pivotal role in creating a resilient manufacturing environment.
Predictive Analytics
Predictive analytics is a specific subset of data analytics that focuses on forecasting future trends based on historical data. For manufacturers, this means not just reacting to demand but predicting it.
Using algorithms and statistical models, predictive analytics processes complex data sets to identify patterns. These patterns can reveal shifts in consumer behavior, allowing firms to adjust their production strategies accordingly. The benefitial aspects of predictive analytics in MRP include:
- Risk management: Understanding potential supply chain disruptions beforehand can minimize impact.
- Cost efficiency: By predicting demand accurately, companies can optimize inventory and reduce wastage.
- Enhanced responsiveness: Companies can swiftly align production schedules with market demand.
Extracting actionable insights from predictive analytics empowers manufacturers to think and act strategically rather than merely managing operational issues as they arise. This paves the way for transformative changes in how resources are planned and utilized.
"Data analytics is not just a tool; it is a catalyst for innovation and growth in manufacturing."
Challenges in Implementing MRP
Implementing Manufacturer Resource Planning (MRP) systems involves various challenges that can significantly impact their effectiveness. Understanding these challenges is crucial for manufacturers looking to adopt MRP successfully. Common problems include human resistance to change, integration complications, and gaps in needed skills and training. These obstacles can hinder operational improvements that MRP is intended to facilitate.
Resistance to Change
Resistance to change is one of the most formidable barriers when implementing MRP. Employees who have worked for long time with established systems or methods may find it difficult to adjust to new procedures. This apprehension can manifest in multiple ways. Resistance might be passive, where employees exhibit indifference, or more active, manifesting as outright refusal to use the new system.
To mitigate this challenge, fostering an environment conducive to change is essential. Here's a few strategies:
- Effective Communication: Inform employees about the reasons for the MRP implementation and its potential benefits.
- Involvement: Engage team members in the planning and implementation processes. Their feedback can make them feel valued and encourage acceptance.
- Support Systems: Create opportunities for team members to share their concerns and receive guidance, easing their transition.
Overcoming resistance facilitates smoother implementation and allows organizations to achieve intended gains with MRP.
Integration Issues
Successful implementation of MRP systems relies heavily on seamless integration with existing infrastructure. Many manufacturers contend with legacy systems that may lack compatibility with modern MRP solutions. This disjoint can create data silos and obstruct vital information sharing, consequently affecting productivity.
Key factors that often contribute to integration issues are:
- Data Quality: The existing data needs to be accurate and consistent for effective integration.
- Infrastructure: Evaluating the readiness of current systems to connect with new MRP software avoids major headaches down the line.
- Stakeholder Communication: Continuous dialogue among IT, management, and staff ensures the alignment of all involved parties.
Integrating MRP with various supply chain components can smooth and enhance the overall production and distribution processes.
Training and Skill Gaps
Proper training is vital in MRP implementation. However, many organizations face challenges reducing skill gaps among their workforce. When staff members do not possess the necessary expertise, the efficacy of the new MRP system is at risk.
Identifying specific training needs is key. Categories for training can encompass:
- Technical Skills: Hands-on learning concerning the MRP software and its complex functionality.
- Process Knowledge: Understanding how MRP interfaces with overall business processes for a holistic approach.
- Continuous Learning Opportunities: Regular training refreshers help ensure staff can keep pace with new updates or versions.
By addressing these gaps through individualized training sessions tailored to comprehension levels, organizations ensure their teams can effectively use MRP systems.
Overall, successfully executing MRP relies on addressing the challenges of resistance to change, integration issues, and training gaps. Prioritizing these facets lays the necessary groundwork for an effective resource planning system.
Benefits of MRP for Manufacturers
Manufacturer Resource Planning (MRP) plays a significant role in enhancing operational capabilities for manufacturers. The correct implementation of MRP can lead to measurable improvements in production processes, inventory management, and customer engagement. Understanding these benefits goes beyond simply acknowledging efficiencies; it involves appreciating how MRP transforms the fabric of manufacturing enterprises.
Improved Efficiency
Efficiency within manufacturing is often gauged by the ability to minimize waste and enhance productivity. By using MRP systems, manufacturers streamline scheduling, ensuring that when raw materials are delivered, they coincide ideally with manufacturing processes. This leads to optimized assembly lines. Efficient timing translates directly into enhanced resource allocation and defined input-output relationships, decreasing turnover time and boosting overall productivity.
Additionally, MRP employs a feedback loop that constantly monitors production outputs against demand. This mechanism allows manufacturers to refine their processes and adjust planning in real-time. These adjustments reduce excess production, which often burdens financial and physical resources. The cyclical efficiency promotes responsiveness to changing market demands, establishing a more resilient organization.
Better Inventory Control
One core aspect of successful manufacturer management hinges on effective inventory control. MRP systems enhance inventory accuracy using integrated systems that provide real-time data tracking. Manufacturers can precisely monitor stock levels, reorder points, and lead times, thus mitigating the risks associated with stockouts or overstock situations. By improving inventory control, resources can be allocated more effectively, supporting just-in-time production practices.
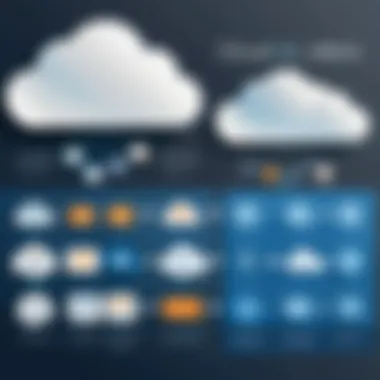
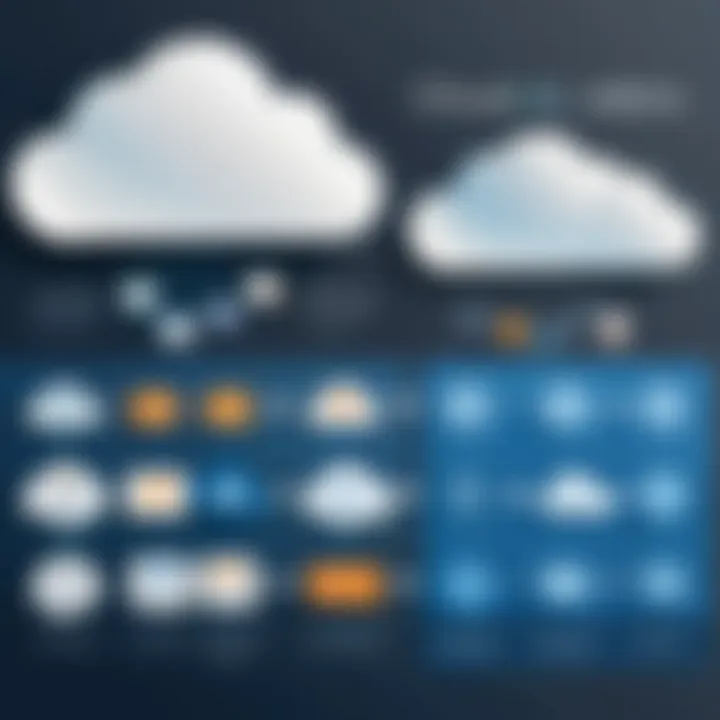
Another advantage of streamlined inventory management is the ability to balance costs. With efficient tracking, manufacturers can reduce carrying costs related to excess stock while ensuring adequate emergency reserves. In summary, well-implemented MRP assures optimal stock levels are maintained without unnecessary financial burden.
Enhanced Customer Satisfaction
In manufacturing, customer satisfaction often correlates to product availability and reliability. MRP systems empower manufacturers to deliver on these customer demands by facilitating timely production schedules and seamless inventory management. The result is a smoother supply chain that improves the rate of timely delivery. Customers experience fewer delayed orders, boosting overall loyalty and satisfaction.
Furthermore, by leveraging the analytics capabilities embedded within MRP systems, manufacturers can forecast demand more accurately. Anticipating shifts in consumer preferences allows proactive production planning. Meeting customer demands without excess waste can foster stronger partnerships and improve brand reputation in the market.
With effective MRP, customer satisfaction is not just an ideal; it becomes achievable due to precise and responsive manufacturing processes.
Future Trends in Manufacturer Resource Planning
Understanding the future trends in Manufacturer Resource Planning (MRP) is essential for manufacturers aiming to remain competitive. The choices made today regarding MRP technology and strategy will shape manufacturing processes for years to come. These trends drive innovation and shape how companies synchronize their resources efficiently.
AI and Machine Learning Integration
The incorporation of Artificial Intelligence (AI) and Machine Learning (ML) into MRP systems presents unprecedented opportunities. AI algorithms can analyze massive heaps of data to forecast demand accurately and optimize inventory levels. With real-time data analysis, manufacturers can make quicker decisions based on changing market needs. This technology effectively reduces errors in production scheduling, thus enhancing normal production flows.
One significant advantage is predictive maintenance, where AI predicts equipment failures before they happen. It saves costs on unexpected repairs. Additionally, the integration of AI alongside traditional MRP methods enhances adaptability. Continuous learning algorithms identify patterns and suggest alert responses to inventory reductions. This minimizes waste and maximizes output efficiency.
Embracing AI and ML is not just a tactical move; it translates into strategic advantages in resource allocation.
Sustainability Considerations
Sustainability has become vital for manufacturers as businesses increasingly focus on environmental responsibility. This approach is also reflected in MRP practices. Future MRP systems will be designed with sustainability considerations as supplemental priorities. For instance, data analytics can help audit supply chains for sustainability practices, ensuring companies adhere to regulations and best practices in resource use.
An example includes selecting materials that minimize environmental impact during production. Emphasizing recyclable and eco-friendly materials demonstrates a firm commitment to sustainability. Furthermore, integrating renewable energy sources like solar power into manufacturing operations also signifies significant risk management and long-term savings.
Ultimately, future MRP systems will need to evolve to support sustainability goals while optimizing operational efficiency. Shortened lead times and reduced resource wastage will become integral components of these systems.
Case Studies of Successful MRP Implementation
The examination of case studies in Manufacturer Resource Planning (MRP) serves as a vital aspect of understanding how theoretical concepts translate into practical applications within various industries. These studies provide valuable insights into the methods, benefits, and potential pitfalls associated with implementing MRP systems. By scrutinizing real-world implementations, professionals can extract lessons applicable to their own contexts, ultimately leading to improved operational efficiency and strategic planning.
Industry Leaders' Approaches
When industry leaders design and execute their MRP systems, they use diverse strategies tailored to their specific operational needs. Major companies like Toyota and Boeing have employed MRP principles with unique approaches to bolster productivity and streamline operations.
One approach adopted by Toyota is the integration of just-in-time (JIT) manufacturing principles with MRP. This supports reducing inventory costs while ensuring that materials arrive precisely when needed in the production process. Toyota's successful implementation showcases the importance of aligning MRP with broader manufacturing philosophies.
Boeing, on the other hand, emphasizes using advanced data integration technologies for their MRP systems. By leveraging data analytics, Boeing can foresee demand fluctuations, manage production schedules effectively and achieve greater precision in resource allocation. This dual approach enables them to maintain a competitive edge in a complex and evolving aerospace market.
Lessons Learned From Implementations
Studying various case studies also reveals critical lessons learned from MRP implementations across sectors. Key insights include:
- Tailoring to Needs: No one-size-fits-all solution exists; customization is essential. Each organization's implementation must reflect its specific objectives and operational context.
- Continuous Training: Training staff on MRP system usage is crucial. Many failures occur due to insufficient skills or understanding of how to leverage new systems effectively.
- Monitoring and Adaptation: Post-implementation evaluation of the MRP systems is necessary for refining them. Organizations must remain open to change, quickly addressing issues as they arise.
- Emphasizing Interdepartmental Communication: Clear communication across departments ensures that all stakeholders in the supply chain understand the MRP processes. Enhanced collaboration can mitigate misunderstanding, resulting in smoother operational flow.
The importance of examining industry case studies is thus multifaceted, aiding professionals in formulating strategies and avoiding common errors while enhancing their implementations of MRP systems for improved efficiency and productivity.
Epilogue
The conclusion of this article encapsulates the entire discussion on Manufacturer Resource Planning (MRP). It serves as a crucial point where the various themes converge, illustrating why MRP is significantly impactful in today's manufacturing landscape. One major element is the notion that MRP is not merely a tool but a strategic framework enabling manufacturers to operate efficiently.
Summary of Key Takeaways
In summarizing our discourse on MRP, several key points emerge that are worth noting:
- Integration of Resources: MRP systems facilitate optimal allocation and utilization of resources.
- Technological Advances: Innovations in technology enhance the capabilities of MRP systems, particularly in data management.
- Efficiency and Cost Reduction: The primary objective of implementing MRP is to boost efficiency and reduce operational costs.
- Real-time Decision Making: Modern systems enable access to real-time data which supports informed decision-making.
- Adaptability: Successful manufacturers utilize MRP as a scalable solution accommodating changing market conditions.
Altogether, these factors reinforce the importance of understanding and implementing MRP effectively to gain a competitive edge.
Future Directions for MRP
Looking ahead, the future of MRP appears to evolve contemporaneously with technology and market demands. Here are some anticipated directions and trends:
- Increased Use of AI: The incorporation of artificial intelligence and machine learning will streamline processes further.
- Focus on Sustainability: There is likely to be an uptick in sustainable practices within the MRP framework, aligning production with environmental considerations.
- Enhanced Collaboration Tools: Rising collaboration tools built into MRP systems will help businesses allow for seamless exchanges across the supply chain.
- Greater Personalization: Future MRP systems may enable more extensive customization options for better alignment with unique business needs.
- Real-time Inventory Management: Systems will increasingly provide real-time inventory visibility, optimizing stock levels more efficiently.
These aspects indicate a promising and transformational future for MRP practices, making it vital for manufacturers to stay attuned to these changes.