Mastering the Fine Line Between Quality Assurance and Quality Control: An In-Depth Analysis
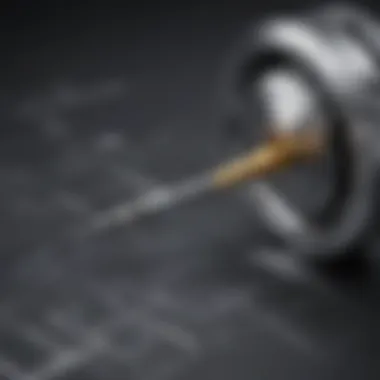

Coding Challenges
Navigating Quality Assurance and Quality Control involves tackling complex challenges to ensure product excellence and customer satisfaction. One of the significant challenges in this domain is striking a balance between quality assurance, which focuses on processes to prevent defects, and quality control, which involves identifying defects through testing and inspection. Understanding the key disparities between these two aspects is crucial for implementing a robust quality management system. By harmonizing quality assurance and quality control, organizations can enhance their overall product quality and meet consumer expectations efficiently.
Meticulous Planning for Seamless Integration
When delving into quality assurance and quality control, meticulous planning is paramount. Careful consideration must be given to the integration of these processes within the existing framework of the organization. It is essential to establish clear protocols and procedures for quality assurance, ensuring that preventive measures are in place to maintain high standards. Simultaneously, quality control mechanisms should be designed to detect and rectify any defects that may arise post-production. By outlining a comprehensive plan that encompasses both quality assurance and quality control, companies can streamline their operations and deliver superior products to their clientele.
Technology Trends
[This section is dedicated to exploring the latest trends in technology that impact quality assurance and quality control methodologies. By delving into emerging technological innovations, readers will gain insights into how new technologies are reshaping the landscape of quality management systems. Expert opinions and analysis provide valuable perspectives on the intersection of technology and quality assurance practices, offering a holistic view of the evolving industry. Stay tuned for in-depth discussions on the technological advancements revolutionizing the QA and QC processes for enhanced efficiency and effectiveness.]
Merging Technology with Quality Management
In the realm of quality assurance and quality control, technology plays a pivotal role in augmenting traditional practices. The advent of cutting-edge technologies such as artificial intelligence, machine learning, and automation have revolutionized the way QA and QC are approached. Leveraging technological tools for predictive analysis, performance monitoring, and defect tracking can significantly improve the overall quality management system. By staying abreast of the latest technological trends and harnessing them effectively, organizations can elevate their quality assurance and quality control methodologies to meet the demands of a dynamic market landscape.
Coding Resources
[Curious about the top resources for enhancing your skills in quality assurance and quality control? This section provides a curated list of programming language guides, tools, and tutorials tailored for aspiring and experienced professionals in the field. Dive into insightful how-to articles, software reviews, and comparisons of online learning platforms to expand your knowledge base and sharpen your QA and QC expertise. Whether you're a seasoned veteran or a novice in quality management, these resources offer invaluable support for your continuous learning journey.]
Empowering Your QA and QC Arsenal
A key aspect of excelling in quality assurance and quality control lies in leveraging the right coding resources. From mastering essential programming languages to exploring innovative tools for quality testing, the abundance of resources available empowers professionals to enhance their skill sets and stay ahead of the curve. By immersing yourself in tutorials, reviews, and practical guides, you can enrich your understanding of QA and QC principles and refine your approach to maintaining product excellence. Stay tuned for comprehensive reviews and recommendations on coding resources that are tailored to meet the diverse needs of QA and QC professionals.
Computer Science Concepts
[Dive deep into fundamental concepts in computer science that underpin quality assurance and quality control practices. Explore the intricate world of algorithms, data structures, artificial intelligence, and networking to gain a deeper insight into the technical foundations of QA and QC. From beginner primers to advanced discussions on quantum computing and futuristic technologies, this section offers a comprehensive exploration of computer science concepts that are essential for mastering quality management systems. Prepare to unravel the complexities of QA and QC through the lens of cutting-edge computer science principles and applications.]
Unveiling the Foundation of Quality Excellence
Enhancing your proficiency in quality assurance and quality control requires a solid understanding of computer science concepts. By delving into the fundamentals of algorithms, AI, and networking, professionals can strengthen their knowledge base and refine their problem-solving skills within the realm of QA and QC. In-depth explorations of emerging technologies and future trends provide a roadmap for integrating advanced computer science concepts into quality management strategies effectively. Stay tuned for a comprehensive breakdown of essential computer science principles that can elevate your expertise in ensuring unparalleled product quality and customer satisfaction.
Introduction
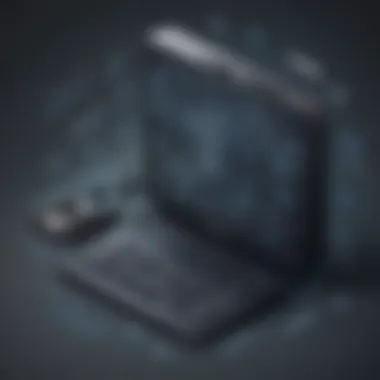
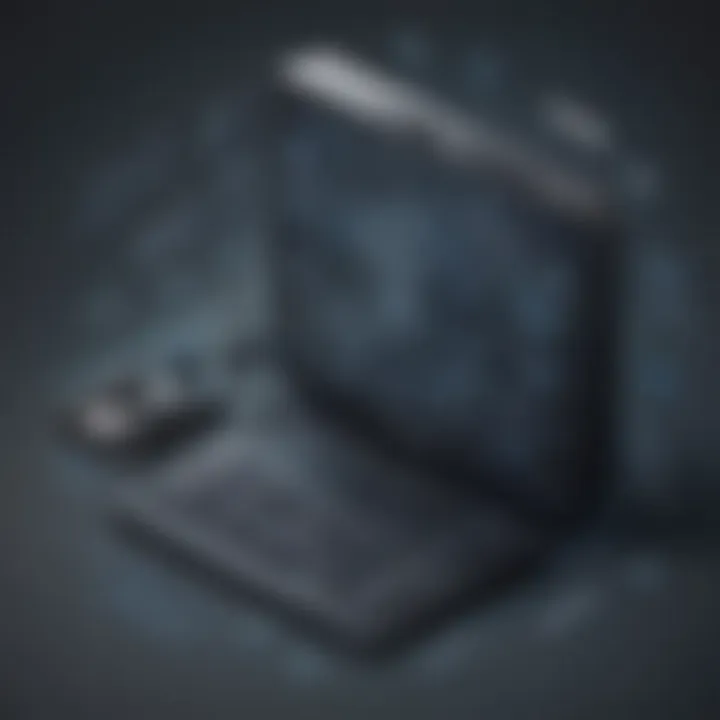
Quality assurance and quality control are essential components in ensuring product excellence and customer satisfaction. As the backbone of quality management systems, understanding the disparities between the two is crucial. Quality assurance involves strategic planning and a proactive approach to maintain high standards throughout the development process. On the other hand, quality control focuses on tactical implementation to inspect and rectify individual product quality. By navigating through these distinct yet complementary realms, businesses can enhance their operational efficiency and customer trust.
Defining Quality Assurance
Quality assurance encompasses the concept of quality in product development, emphasizing the adherence to predefined standards and procedures throughout all stages. This strategic approach ensures that products meet established criteria, enhancing reliability and consistency. The concept of quality in product development directs attention towards preventing defects rather than rectifying them post-production, aligning with the proactive nature of quality assurance. Its core characteristic lies in its ability to continuously evaluate and refine processes, leading to enhanced product quality and reduced risks.
The strategic approach of quality assurance emphasizes the systematic management of quality throughout the product development life cycle. By integrating QA principles into every phase, organizations can identify potential issues early and implement corrective measures promptly. This approach aims to instill a culture of quality within the organization, emphasizing prevention over correction. While its unique feature lies in its focus on prevention, it may require significant initial investment but yields long-term benefits, such as improved customer satisfaction and brand loyalty.
Exploring Quality Control
Maintaining quality standards forms the bedrock of quality control, ensuring that products meet specified requirements and criteria. The essence of maintaining quality standards involves meticulous inspection and testing to detect and rectify deviations from set benchmarks. This key characteristic of quality control underscores its significance in upholding product quality and customer satisfaction. One unique feature of this aspect is its immediate impact on product quality, as it involves real-time monitoring and adjustments to prevent defects.
The tactical implementation of quality control revolves around the practical execution of quality standards and procedures. By applying specific techniques and methodologies, organizations can verify product quality and address discrepancies efficiently. The tactical approach emphasizes the importance of product-oriented inspection and intervention to meet defined quality objectives. Its unique feature lies in its ability to swiftly identify and resolve quality issues, ensuring that products conform to set specifications and exceed customer expectations.
Differentiating QA and QC
Quality Assurance (QA) and Quality Control (QC) are critical components in ensuring product excellence and customer satisfaction. Quality Assurance focuses on preventing issues before they occur, emphasizing a strategic approach to quality in product development. On the other hand, Quality Control concentrates on maintaining quality standards through tactical implementation, ensuring products meet predefined criteria. Understanding the disparities between QA and QC is fundamental in establishing a robust quality management system.
Purpose and Focus
Preventative vs. Corrective Measures
When comparing Preventative and Corrective Measures, it's essential to note their distinct contributions to quality management. Preventative measures aim to identify and address potential issues before they impact product quality. This proactive approach enhances efficiency and reduces the likelihood of defects, aligning with the preventive nature of QA. On the other hand, Corrective Measures come into play after defects are identified, focusing on rectifying issues to meet quality standards. While corrective actions are vital in QC processes, preventive measures play a crucial role in QA by addressing root causes and preventing future occurrences. Both approaches are complementary, emphasizing the importance of a well-rounded quality management strategy.
Process-oriented vs. Product-oriented
In distinguishing between Process-oriented and Product-oriented approaches, the emphasis shifts towards the nature of evaluation and improvement. Process-oriented QA focuses on optimizing processes and workflows to enhance overall quality at every stage of production. By continuously refining procedures, organizations can achieve consistency and efficiency in delivering high-quality products. On the other hand, Product-oriented QC centers on inspecting individual products to identify and rectify defects, ensuring adherence to predefined quality standards. While process-oriented approaches prioritize systemic enhancements, product-oriented strategies concentrate on verifying conformance at a product level, reflecting the integrated nature of QA and QC in quality management.
Scope of Activities
Comprehensive System Evaluation vs. Individual Product Inspection
The comparison between Comprehensive System Evaluation and Individual Product Inspection provides insights into the breadth and depth of quality assessment. Comprehensive System Evaluation involves analyzing entire systems and processes to identify areas for improvement and optimization. This holistic approach aligns with QA objectives, emphasizing continuous improvement and systemic enhancements. In contrast, Individual Product Inspection focuses on scrutinizing specific products to detect deviations from quality standards and ensure product reliability. While system evaluations contribute to strategic decision-making, product inspections play a crucial role in verifying quality at a granular level, underscoring the relationship between comprehensive evaluations and detailed inspections in quality management.

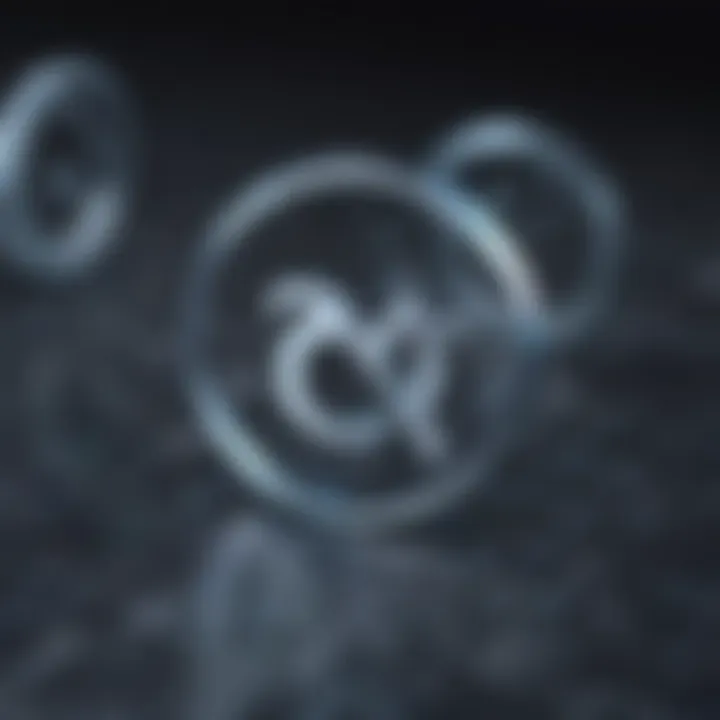
Continuous Improvement vs. Defect Identification
Drawing a distinction between Continuous Improvement and Defect Identification illuminates the strategic focus of quality enhancement. Continuous Improvement involves ongoing efforts to refine processes, implement best practices, and drive innovation across the organization. This iterative approach to quality aligns with the quality assurance framework, fostering a culture of excellence and efficiency. In contrast, Defect Identification centers on detecting and rectifying deviations from quality standards, minimizing defects and ensuring product compliance. While continuous improvement drives organizational growth, defect identification ensures adherence to quality benchmarks, showcasing the complementary nature of improvement initiatives and defect resolution in optimizing quality outcomes.
Implementing QA and QC
In this article, the section discussing Implementing QA and QC portrays a critical aspect of quality management in product development. Implementing QA and QC is essential in ensuring that the products meet the desired quality standards and customer expectations. This process involves integrating quality assurance practices with quality control measures to maintain consistency and reliability in product outcomes. By implementing QA and QC effectively, organizations can streamline their operations, identify potential issues early, and enhance overall product quality.
Integration in Quality Management
The synergy between assurance and control
The synergy between assurance and control is a pivotal concept in quality management, emphasizing the collaborative relationship between ensuring quality (QA) and controlling quality (QC). This integration allows companies to proactively address quality issues before they escalate, fostering a culture of continuous improvement and customer satisfaction. The key characteristic of this synergy lies in its ability to combine preventative measures with corrective actions, creating a robust quality management system. By leveraging the synergy between assurance and control, organizations can optimize their processes and deliver high-quality products consistently.
Strategies for seamless incorporation
Strategies for seamless incorporation encompass the methodologies and practices adopted to integrate QA and QC seamlessly into the existing system. These strategies focus on aligning quality objectives with overall organizational goals, ensuring that quality remains a top priority at every stage of the product lifecycle. One key characteristic of these strategies is their adaptability to diverse industry sectors, allowing companies to tailor quality management processes to suit specific requirements. The unique feature of these strategies lies in their emphasis on proactive problem-solving and risk mitigation, empowering organizations to pre-emptively address quality concerns and drive continuous improvement.
Tools and Techniques
Software for QA automation
Software for QA automation is a technological innovation that enhances the efficiency and accuracy of quality assurance processes. This tool automates repetitive tasks, reduces human error, and accelerates testing procedures, enabling organizations to deliver high-quality products faster. The key characteristic of this software lies in its ability to generate detailed reports and analytics, providing valuable insights into product quality and performance metrics. The unique feature of software for QA automation is its capacity to optimize testing resources and increase test coverage, resulting in more thorough quality assessments.
Statistical methods for QC analysis
Statistical methods for QC analysis play a vital role in assessing the quality of products through data analysis and interpretation. These methods enable organizations to identify trends, patterns, and anomalies in product performance, facilitating informed decision-making and problem-solving. The key characteristic of statistical methods for QC analysis is their quantitative approach to quality evaluation, allowing for objective and measurable assessments of product conformance. The unique feature of these methods lies in their ability to detect outliers and deviations, enabling organizations to address quality issues promptly and effectively.
Monitoring and Evaluation
Key performance indicators for QA success
Key performance indicators (KPIs) for QA success are metrics used to measure the effectiveness and efficiency of quality assurance processes. These indicators provide valuable insights into the performance of QA activities, highlighting areas of strength and improvement opportunities. The key characteristic of KPIs for QA success is their ability to align quality goals with organizational objectives, ensuring that QA efforts contribute to overall business success. The unique feature of these indicators lies in their capacity to track quality-related metrics in real-time, enabling organizations to make data-driven decisions and enhance quality outcomes.
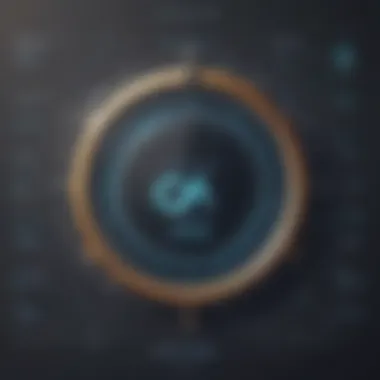

Defect tracking for QC efficacy
Defect tracking for QC efficacy involves recording and monitoring product defects to improve the quality control process. By documenting defects, organizations can analyze the root causes of issues, implement corrective actions, and prevent future occurrences. The key characteristic of defect tracking lies in its focus on continuous improvement and defect prevention, driving QC processes towards excellence. The unique feature of this approach is its ability to create a feedback loop for quality improvement, enabling organizations to iteratively enhance product quality and customer satisfaction.
Ensuring Excellence and Customer Satisfaction
In this section of the article, we delve into the crucial aspects of ensuring excellence and customer satisfaction within the realm of quality assurance and quality control. This topic holds utmost importance as it directly impacts the overall success and reputation of a product or service. By focusing on specific elements such as product quality and customer experience, businesses can elevate their offerings to meet and exceed consumer expectations.
The Impact on Product Quality
Enhanced Product Reliability and Consistency
Now, let's dissect the concept of enhanced product reliability and consistency. This aspect plays a pivotal role in establishing a strong foundation for a product in terms of its performance and longevity. The key characteristic of enhanced product reliability and consistency lies in its ability to deliver a consistent and dependable experience to end-users. This reliability not only boosts customer confidence but also fosters repeat purchases and positive word-of-mouth. Despite its undeniable benefits, there might be challenges associated with overreliance on a specific product feature, which may lead to complacency in innovation and adaptation.
Risk Mitigation and Cost Reduction
On the other hand, risk mitigation and cost reduction are fundamental components that contribute significantly to product quality. By identifying and preemptively addressing potential risks, businesses can safeguard their products against unforeseen challenges and uncertainties, ultimately enhancing overall quality. The key characteristic of risk mitigation and cost reduction is their ability to streamline processes, optimize resources, and minimize financial burdens. While these strategies offer substantial benefits such as improved efficiency and profitability, there may be limitations in terms of initial investment requirements and potential trade-offs between cost savings and product innovation.
Enhancing User Experience
Meeting Customer Expectations
Turning our attention to meeting customer expectations, we underscore the importance of aligning product offerings with the desires and requirements of the target audience. By prioritizing customer-centric approaches, businesses can create products that resonate with users, fostering satisfaction and loyalty. The key characteristic of meeting customer expectations is its ability to establish strong emotional connections with consumers, driving long-term brand affinity and advocacy. However, businesses must be cautious of potential drawbacks such as overcustomization, which could lead to increased complexities and reduced scalability.
Building Brand Trust and Loyalty
Lastly, building brand trust and loyalty emerges as a critical factor in enhancing user experience. By cultivating trust through consistent delivery of quality products and exceptional services, businesses can nurture enduring relationships with customers. The key characteristic of building brand trust and loyalty is its capacity to create lasting brand advocates who promote the business through positive reviews and recommendations. While this strategy can bolster brand reputation and customer retention, there may be challenges related to maintaining trust in the face of market fluctuations and competitive pressures.
Conclusion
In the realm of quality management, the conclusion serves as the pivotal reflection of the synergistic relationship between quality assurance (QA) and quality control (QC) practices, providing a comprehensive overview of their collaborative efforts in fostering product excellence and ensuring customer satisfaction. The conclusion encapsulates the essence of integrating QA and QC into a unified quality management system, emphasizing their indivisible roles in upholding high-quality standards throughout the product development lifecycle. Awareness of the distinct yet interdependent functions of QA and QC enables organizations to streamline processes, detect deviations promptly, and continuously enhance product quality. Moreover, the conclusion acts as a compass for organizations seeking to fortify their brand reputation, mitigate risks, and drive cost efficiencies through a proactive QA and QC approach.
Harmonizing QA and QC Practices
The symbiotic relationship for quality management
The symbiotic relationship between QA and QC within quality management embodies a pivotal aspect of operational excellence. This interconnectedness highlights the interwoven nature of preventive QA measures and corrective QC actions in nurturing a culture of quality within an organization. By fostering collaboration between these functions, organizations can optimize resource utilization, minimize rework, and accelerate time-to-market. The inherent characteristic of mutual dependency between QA and QC underscores the shared goal of enhancing product quality and customer satisfaction. This symbiosis cultivates a dynamic environment where continuous improvement becomes not just a goal but a foundational principle driving organizational success. The unique feature of this relationship lies in its ability to bridge the gap between proactive quality assurance practices and reactive quality control measures, creating a harmonious yin-yang equilibrium that fortifies the product development landscape.
Continuous improvement through collaborative efforts
Continuous improvement through collaborative efforts epitomizes the ethos of perpetual evolution ingrained in effective quality management strategies. This aspect underscores the significance of embracing a culture of continuous learning, experimentation, and adaptation to refine existing processes and innovate new solutions. By encouraging cross-functional collaboration and knowledge-sharing, organizations can harness diverse perspectives to drive sustainable quality improvements. The key characteristic of this approach lies in its iterative nature, where feedback loops and data-driven insights fuel iterative enhancements across QA and QC dimensions. The collaborative ethos fosters a culture where shared goals, transparent communication, and collective accountability propel teams towards achieving excellence. While the advantages of continuous improvement through collaboration are evident in accelerated problem-solving, optimized workflows, and enhanced product outcomes, organizations must remain cognizant of potential challenges such as resistance to change, siloed mindsets, and resource constraints. However, the transformative potential of this approach in cultivating a culture of innovation, resilience, and customer-centricity underscores its indispensable value within the realm of quality management.